The rubber transfer molding machine (KAUÇUK TRANSFER PRESS MAKİNESİ) is ideal for the production of solid rubber parts, rubber parts with inserts, and parts that require bonding rubber to metal. Rubber transfer molding combines the advantages of injection rubber molding with the ease of compression molding. This process is most often used for forming rubber products that require:
- Exact positioning
- Bonding rubber to metal parts
- Mold designs that contain multiple cavities and can trap air
- Intricate parts with lower volume requirements
The rubber transfer molding machine sometimes can also be regarded as an economic replacement type injection molding machine,because its manufacturing cost is lower than injection molding machine,so to adopt the transfer molding machine not only can realize the purpose of making rubber parts by injection way,but can also save investment cost for machines.
Advantages of Transfer Molding Process:
1. Transfer Molding cycle time is shorter than Compression Molding cycle (but longer than Injection Molding cycle)
2. The transfer molding method is capable to produce more complicated shapes than Compression Molding.
3. Maintaining closer dimensional tolerances than compression molding.
4. Provides uniformity among the molded products.
5. Fast mold setup.
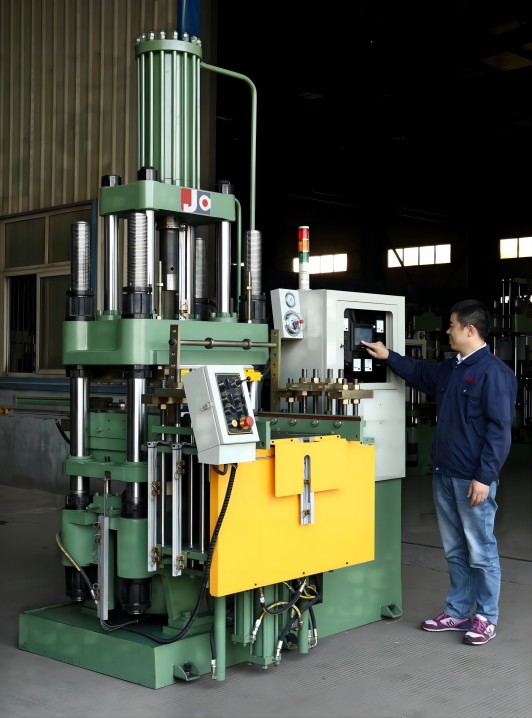
Work flow:
The process of transfer molding process:
Pushing unvulcanized rubber through the sprue into a heated mold. Similar to compression molding, transfer molding also requires raw material preparation into rubber pellets and/or rubber preforms.
Instead of placing the rubber preforms in the mold cavity, the preforms are placed in a barrel “pot” at the top of the mold .And then,the plunger, mounted on the top plate, moves downwards, pressing on the rubber and forcing it to fill the mold cavity below through the sprue.
During the curing process, the plunger is kept in place until the preform takes on the shape of the mold and the rubber is vulcanized. Once the part cures, hardens, cools, it is then ejected. Any excess cured rubber left in the pot is removed and the mold cavities are cleaned for the next molding cycle to begin.
Transfer Molding for Rubber to Metal Bonding Process:
Transfer molding is an effective solution for rubber to metal bonding process, the metal components are loaded into a heated mold either by hand or using a loading fixture. Rubber material is then loaded into the charge pot of the transfer mold. While the mold closes, the rubber is heated and then transferred through the sprue into the mold cavities and distributed around the metal insert. With the pressure and elevated temperatures, the rubber cures and vulcanizes, allowing the parts to be removed.
Technical Specification:
Model |
JC-YCB63T |
JC-YCB100T |
JC-YCB200T |
JC-YCB300T |
JC-YCB350T |
JC-YCB500T |
Tonnage |
63T |
100T |
200T |
300T |
350T |
500T |
Max.system pressure |
21 Mpa |
21 Mpa |
21 Mpa |
21 Mpa |
21 Mpa |
21 Mpa |
Rapid Clamping speed |
≥60mm/s |
≥60mm/s |
≥60mm/s |
≥60mm/s |
≥50mm/s |
≥50mm/s |
Platen size(mm) |
350x350 400x400 |
450x450 500x500 |
510x540 600x550 |
700x650 |
700x700 |
700x700 800x800 950x800 |
Max.daylihgt opening(mm) |
350 |
350 |
400 |
400 |
400 |
400 |
Max.temperature(℃) |
250 |
250 |
250 |
250 |
250 |
250 |
Material barrel size(mm) |
φ70x215 |
φ80x255 |
φ90x290 |
φ110x355 |
φ110x355 |
φ130x445 |
Injection pressure (Mpa) |
60 |
60 |
60 |
100 |
100 |
100 |
Injection stroke(mm) |
320 |
350 |
380 |
450 |
450 |
580 |
Max.ejector force |
60KN |
60KN |
60KN |
100KN |
100KN |
100KN |
Ejector mechanism (optional) |
2TR/3RT/4RT |
2TR/3RT/4RT |
2TR/3RT/4RT |
2TR/3RT/4RT |
2TR/3RT/4RT |
2TR/3RT/4RT |
Ejector stroke(mm) |
250 |
250 |
300 |
350 |
400 |
450 |
Motor power(KW) |
5.5 |
5.5 |
7.5 |
7.5 |
11 |
13 |
Heating power(KW) |
9.6 |
9.6 |
18.6 |
20.6 |
20.6 |
27.8 |
Dimension(LxWxH:mm) |
1600x1900x3000 |
1700x2100x3100 |
1950x2300x3250 |
2150x2600x3900 |
2550x3600x5250 |
2750x4200x5950 |
Oil tank capacity(Liters) |
160 |
270 |
320 |
350 |
400 |
600 |